Una tecnología española repara buques de la Armada estadounidense mientras navegan
En Meltio casi han duplicado su facturación en un año y han pasado de 80 a más de 125 empleados
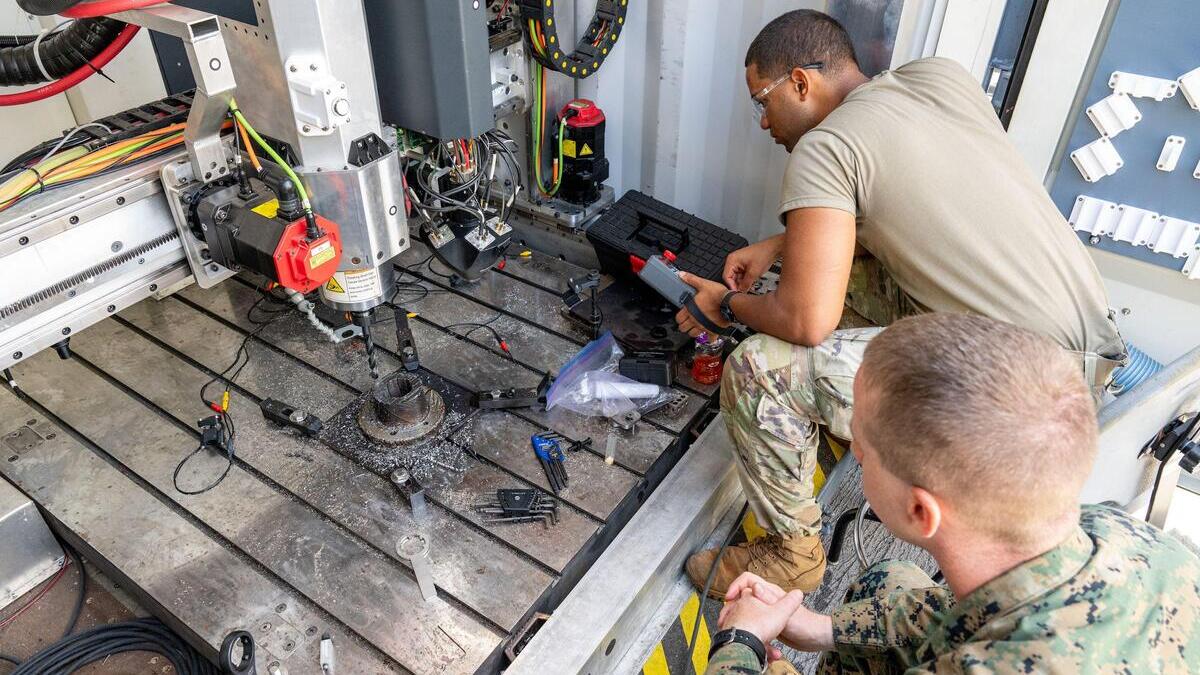
La tecnología española que repara buques de la armada estadounidense mientras navegan. | Meltio
Les salvó la tecnología española. No de un naufragio, pero sí de pasar un mal rato enorme. El USS Somerset de la Armada estadounidense se encontraba en plenos ejercicios navales, rodeados de más buques, y sufrió una avería sensible: la de la bomba que genera el agua potable a bordo. El problema lo solucionó un dispositivo hecho en Linares (Jaén).
Las operaciones navales son complejas y a menudo se llevan a cabo lejos de los sistemas de apoyo en tierra. Los fallos de los equipos en estos entornos pueden tener graves consecuencias, en especial si se trata de sistemas críticos. Pocas horas tras iniciar su despliegue, la bomba de ósmosis inversa que surte del líquido elemento a todos los servicios y marinería del buque se rompió.
En condiciones normales, sin agua potable a bordo, tendrían que haber echado mano de ayuda externa o abandonado la formación para su reparación. Sustituir una pieza de este tipo supondría esperar días o incluso semanas a que llegara un repuesto a través de las cadenas de suministro establecidas. Este retraso podría haber hecho descarrilar la misión de Somerset. Sin embargo, la repararon en un tiempo récord con la ayuda de una tecnología traída del futuro: la impresión 3D con metal, a base de derretirlo con láser.
La empresa jiennense Meltio es la que ha dado una vuelta de tuerca a su tecnología para resolver problemas de este tipo en barcos de la armada en plena navegación. Si hasta ahora eran necesarias soldaduras manuales para restañar piezas rotas, muchas de ellas a realizar en astilleros, ahora se pueden realizar por fusión de metal robotizado durante sus despliegues.
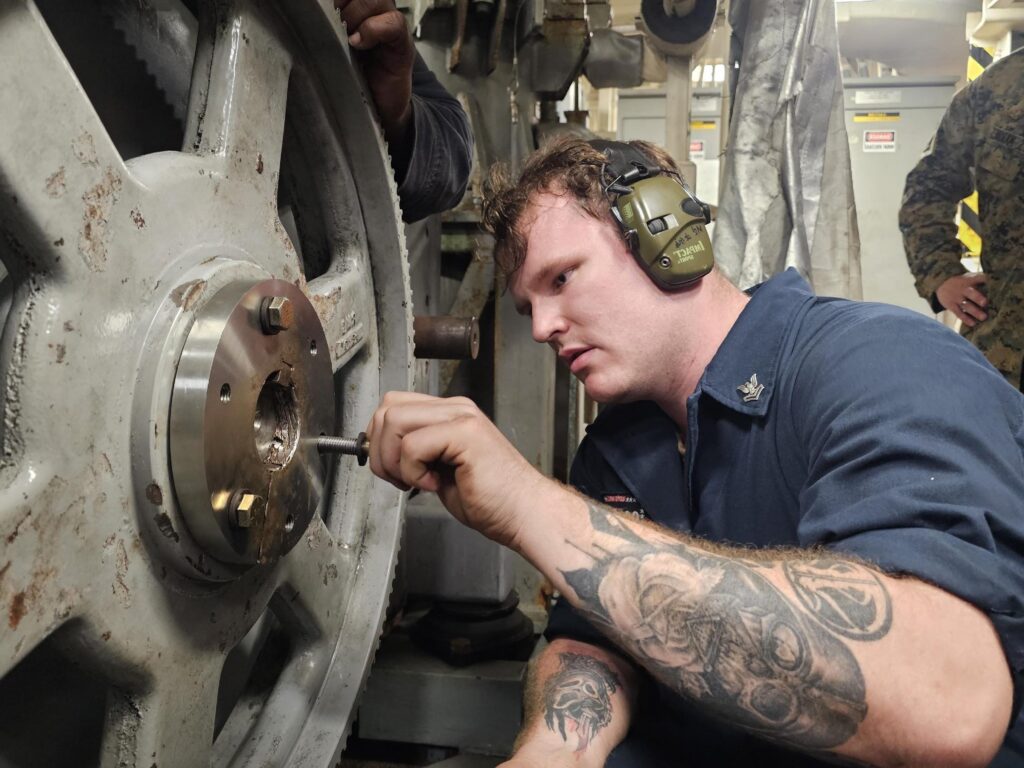
La compañía andaluza ya puso sus pies en la US Navy con una solución única: su cabezal láser, capaz de disparar sus ocho haces de luz sobre casi cualquier metal, para generar piezas al estilo de una empresa 3D. Puede ser un grifo, el tirador de una puerta, un cerrojo, o una hélice.
Una máquina computarizada tipo CNC armada con un brazo robótico va moviendo su cabezal, que derrite un largo hilo de acero, cobre o aluminio —por poner unos ejemplos—, y genera la pieza deseada. Lo hará siguiendo las pautas marcadas por su correspondiente archivo digital, con sus formas y medidas, que será descargado de un repositorio en la nube binaria.
Ahora, Meltio ha colocado una versión más avanzada de su sistema en el USS Somerset, un buque anfibio propiedad del Pentágono. La función a cumplimentar no será crear nuevas piezas, sino restaurar otras que hayan fallado, se hayan agrietado o hayan perdido sus cualidades debido al desgaste o la corrosión.
Hasta ahora esto recaía en marineros expertos en soldadura o forja, pero al final el resultado dependía de sus manos. Esto conducía de manera frecuente a imprecisiones, las debilidades propias de un trabajo no mecanizado y lejos de unas instalaciones especializadas. Ahora es un ordenador el que dirige y ejecuta los comandos automatizados para restaurar las piezas dañadas.
Los militares son poco dados a comentar sus procesos operativos, aunque se sabe que este método, u otros similares, están siendo usados por Rusia, Israel y algunas marinas adscritas a la OTAN. La marina francesa tiene instalados sistemas de impresión Meltio en el portaaviones Charles de Gaulle y han estado haciendo pruebas en su base de Tolón. Con una impresora 3D dotada de este cabezal, crearon desde cero una tubería muy especializada en un tiempo razonable.
Dos caminos distintos
Existen dos formas de generar piezas metálicas de manera aditiva. Una es a base de polvo metálico, pero el proceso es lento, costoso, y se requiere de una atmósfera industrial muy específica, con alta protección a sus operarios. Los restos del proceso son altamente tóxicos, y no se puede ejecutar en cualquier sitio. El otro es el de la creación 3D, y es más sencillo, rápido y llevadero.
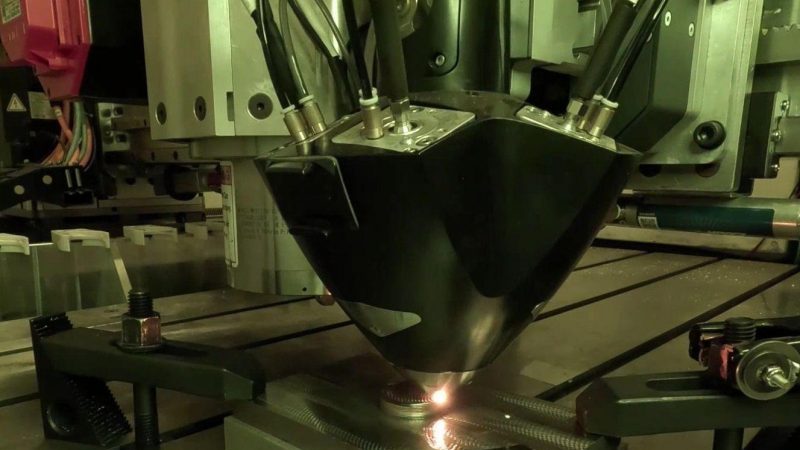
La diferencia estriba en que el primero es mucho más preciso, aunque no siempre es necesario el grado de detalle que aporta. Es perfecto para piezas muy pequeñas, como las de joyería, elementos aeronáuticos, o médicos que quepan en la palma de una mano.
El segundo es más rápido, sencillo, y puede generar piezas muy grandes en periodos de tiempo mucho más cortos. La impresión metálica de una pieza tarda entre cuatro y diez horas, y si se trata de una pieza muy grande, puede tardar algunas horas más; la basada en polvo de metal, puede tardar varios días, y hasta una semana.
La necesidad dictamina el proceso
Este segundo tipo es mucho más adecuado para las necesidades de los navíos militares, que buscan la manera de no depender de parar en puerto para este tipo de trabajo. La meta última no es otra que prolongar los periodos de servicio en el mar. Los buques militares pueden estar meses navegando, y tan solo están limitados por los víveres y combustible que consuman, que puede ser izado a bordo desde otros navíos.
Estos ciclos previstos pueden variar en el momento en que tengan que llegar a puerto a realizar reparaciones, pero si las pueden hacer durante la navegación, ganan en autonomía, flexibilidad y sin depender de proveedores, existencias y su logística añadida.
Los militares rara vez compran productos que se les ofrecen sin validar su funcionamiento en un prolongado proceso de pruebas. Lo que están haciendo en el USS Bataan y el USS Somerset no es otra cosa que una fase inicial de validación del sistema. Si va pasando los aprobados, más tarde acaba saliendo a concurso público y a partir de ahí, los mecanismos se incorporarían a muchas más embarcaciones una vez adquiridos.
Todo cabe en un contenedor pequeño
A nivel mecánico, la impresora 3D que equipa el cabezal de Meltio viaja en un contenedor náutico cerrado y dotado de una atmósfera inerte. A los militares les gusta porque es relativamente manejable, y su operativa casa con el tamaño y posibilidades de sus sistemas. Si pasan todas las pruebas, a la compañía ubicada en Linares, Jaén, se le abrirán las puertas del entorno OTAN, con todo lo que ello conlleva.
En apenas un año casi han duplicado su facturación, han pasado de 80 a más de 125 empleados, y aglutinan técnicos e ingenieros de 15 nacionalidades. Su crecimiento es exponencial, y apenas tienen competencia con su cabezal patentado de ocho láseres concentrados; hay otros sistemas parecidos, pero no son como este.